Yutung Industrial Customize Roto Moulding (rotational moulding) products. But what is roto moulding?
What is roto moulding?
Rotational moulding, also known as rotational molding, rotational molding, rotary molding, roto moulding etc.
It is a hollow molding method for thermoplastic plastics. This method is to first add plastic raw materials into the mold, and then the mold is continuously rotated along two vertical axes and heated. Under the action of gravity and heat energy, the plastic raw materials in the mold are gradually and evenly coated, melted and adhered to the mold cavity.
The entire surface is formed into the required shape, and then cooled and shaped to form the finished product.
Process Principle
The basic process of rotational molding is very simple, which is to place powdered or liquid polymer in a mold, heat it while the mold rotates and revolves around a vertical axis, and then cools to form.
At the beginning of the heating stage, if a powdery material is used, a porous layer is first formed on the surface of the mold, and then gradually melts during the circulation process, and finally a homogeneous layer of uniform thickness is formed; if a liquid material is used, a porous layer is first formed on the surface of the mold.
Coated on the mold surface, flow stops completely when the gel point is reached. The mold is then transferred to the cooling area, cooled by forced ventilation or water spray, and then placed in the work area, where the mold is opened and the completed parts are removed, and then the next cycle is carried out
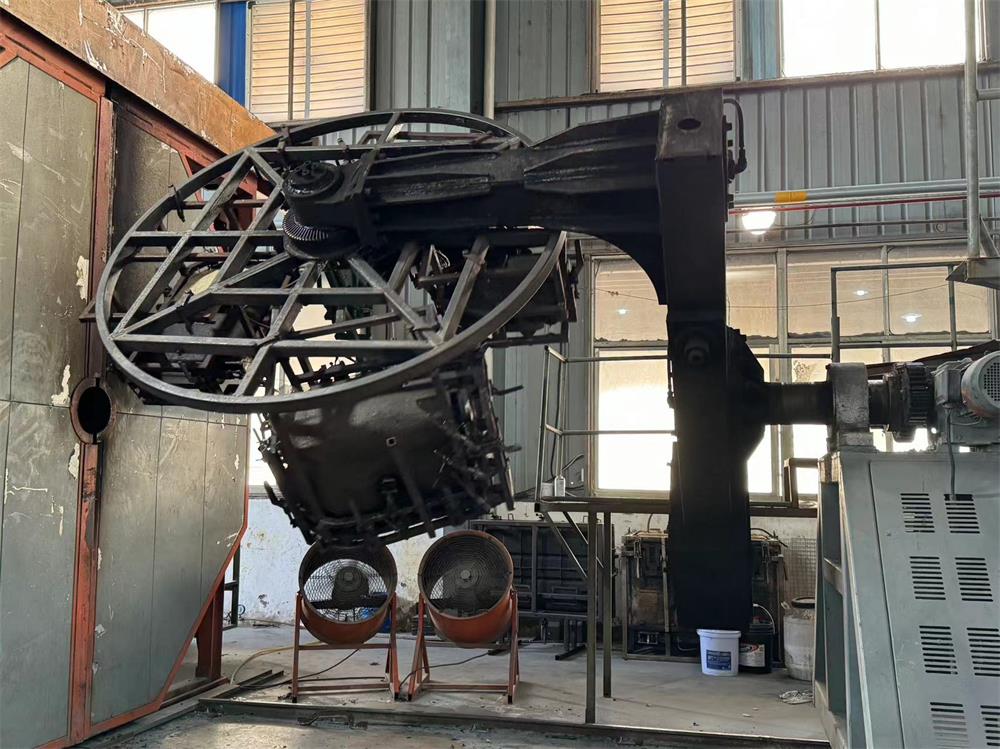
Cooling Machine
Features
In terms of Forming Ability
- The wall thickness of the product is uniform, with no corner waste and no welds; products with a wide range of wall thickness can be formed, such as polyethene rotational molding parts, and the wall thickness can range from 1 to 16mm. However, due to the viscosity, it is difficult to form thick-walled products. The rotational molding process is particularly suitable for molding 2~5mm plastic products.
- Usually, only hollow products or shell products can be produced, and it is difficult to process solid products. Moreover, the surface condition of the product is highly dependent on the surface of the mold cavity.
- The dimensional accuracy of rotationally formed products is low, and its dimensional accuracy is usually ±5%.
In terms of Forming Process
- Suitable for molding large and extra-large parts. Since the rotational molding process only requires that the frame be strong enough to support the weight of the material, mold, and frame itself, as well as the mold closing force to prevent material leakage, there is no need to use very bulky equipment and molds even when processing large and extra-large plastic parts. . Therefore, in theory, there is almost no upper limit on the size of products made by rotational molding.
- Suitable for the production of multiple varieties and small batches of plastic products – because the mold used for rotational molding has a simple structure and low price, it is very convenient to change products.
- Suitable for processing large hollow products with complex shapes, which is unmatched by other molding processes.
- It is easy to change the color of plastic products. When the color of the product needs to be changed, the molding mold only needs to be cleaned.
- The main disadvantages of rotational molding are large energy consumption because, in each molding cycle, the mold and mold base need to undergo repeated heating and cooling; the molding cycle is long because the plastic mainly conducts heat under static conditions, so the heating time of rotational molding is long; the labor intensity is high, and the dimensional accuracy of the product is poor.
Manufacturing Process
The basic process of rotational molding is very simple, which is to place powdered or liquid polymer in the mold, heat it and rotate it around two vertical axes (rotation and revolution).
Coating release agent:
Coating release agent on the mold is to facilitate the removal of the product from the mold, and at the same time, it can effectively avoid damage to the product during demoulding due to the strong adhesion between the product and the mold.
Install inserts and related molding accessories:
Inserts mainly play the role of local reinforcement of parts. Molding accessories are mainly modules used to point out ribs or special parts for molding. They must be properly installed in the newly set position before adding materials to the mold. superior.
Loading:
Strict measurement should be carried out before adding materials. When additives need to be added, the relevant components need to be premixed. Accurately weigh the powdered resin required for the final part, add it to the bottom of the separate mold, then fasten the two halves of the mold together and install them on the bearing shaft;
Mold closing:
Before closing the mold, pay attention to remove the remaining material at the mold closing area, and ensure that the two parting surfaces are tightly sealed to avoid material leakage during processing;
Heating:
Put the mold filled with materials into the heating furnace (or heat it with a gas flame or other heat source). The temperature of the heating furnace is set above the melting point of the resin, and the frame simultaneously rotates around the main and auxiliary axes that are perpendicular to each other. During the rotation process, the mold is heated to a given temperature and then kept warm. The material gradually melts under rotation and heating, settles on the entire inner wall of the mold cavity, and gradually removes the gas trapped in the material until the finished part is formed.
Cooling and shaping:
When the resin is fully melted, transfer the mold to the cooling chamber and cool it, where it continues to rotate while being cooled by forced ventilation or water spray.
Demolding and cleaning the mold:
The former is to avoid damaging the product during demoulding, and the latter is to remove the remaining materials and debris on the mold to prepare for the next molding cycle.
Application
With the development of rotational molding technology, the application scope of its products continues to expand. The application range of rotational molding products has been very wide. Some representative applications can be exemplified as follows.
- Container-type rotational molded parts. These plastic parts are widely used in water storage tanks, storage tanks for various liquid chemicals (such as acids, alkalis, salts, chemical fertilizers, pesticides, etc.), gasoline containers (gasoline storage tanks) and fuel tanks for automobiles and aircraft), battery casings, etc.
- Rotary molded parts for automobiles mainly use polyethylene and polyvinyl chloride paste resin to rotomold various pipe fittings, such as air-conditioning elbows, backrests, armrests, etc.
- Sports equipment and various substitutes. There are mainly various parts made of polyvinyl chloride paste rotational molding, such as water balloons, floats, bicycle seat cushions, boats, and shock absorbers between boats and docks. Rotational cross-linked polyethylene barrels made from Philips’ rotomolding grade cross-linked polyethylene tree “Maricxcl-100” can compete with metal barrels, and they have good chemical resistance and low maintenance costs. Rotational molded pallets were commercialized in the United States, Japan and other countries in the early 1970s; surfboards, boats, etc. are also rotational molded parts often mentioned in the literature.
- Toys, models, handicrafts, etc. Since rotational molding molds can be manufactured by precision casting, electroforming and other processes; the surface of the rotomolded parts has a very good “replication” effect on the fine structure of the mold cavity surface, so the rotomolding method can make the product quite delicate and beautiful, so it is commonly used Used to produce products with greater ornamental value, especially toys, models, handicrafts, etc.
- In addition to the above, rotational molding products are widely used in various boxes, shells, large pipes and other products, such as turnover boxes, garbage bins, machine casings, protective covers, lampshades, bathrooms, toilets, telephone rooms, and yachts. etc. Rotational molding products have been widely used in liquid chemical storage and transportation, washing tanks, reaction tanks, etc. in chemical enterprises, industrial coatings, rare earth production, as well as river and sea buoys, domestic water tanks and other fields.
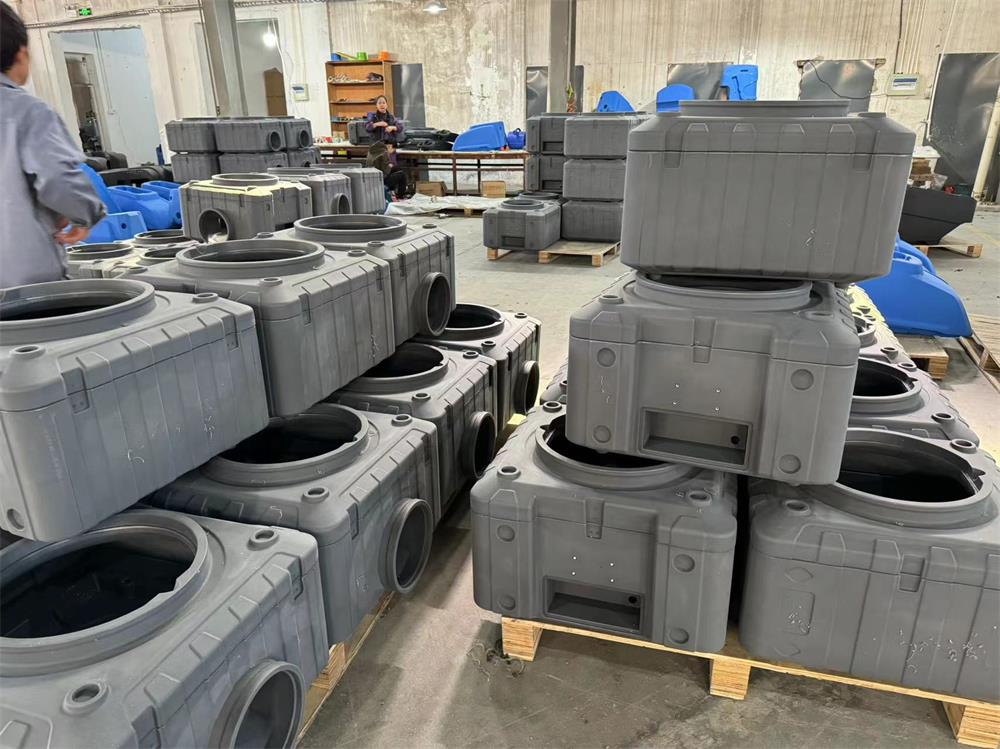
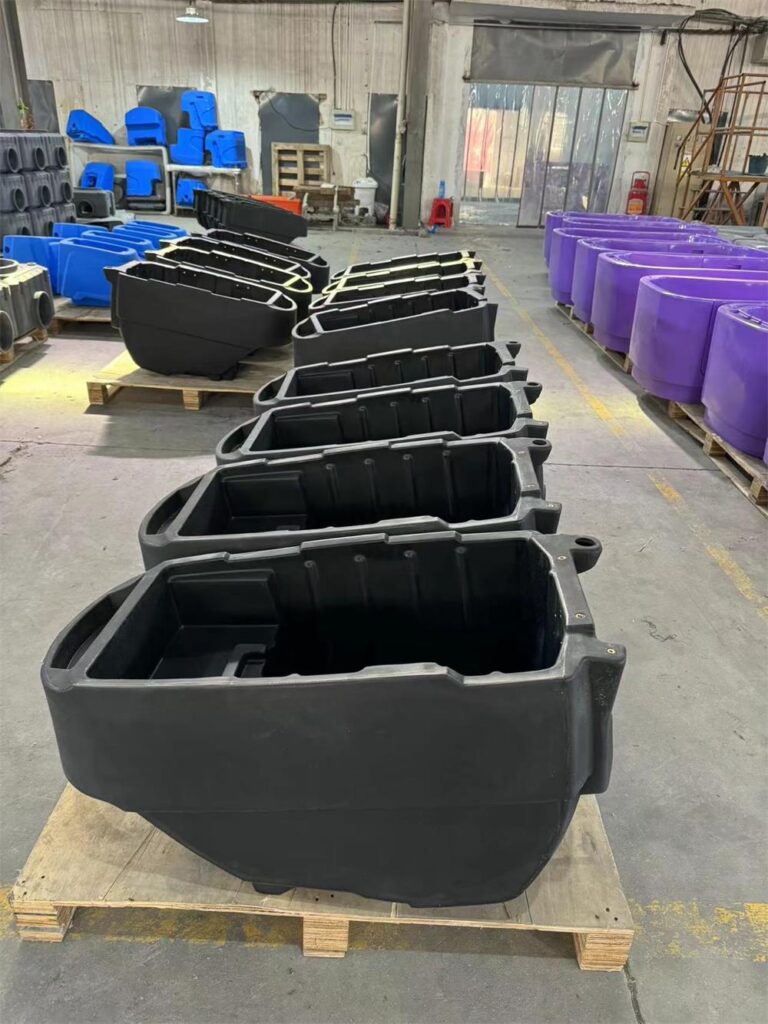
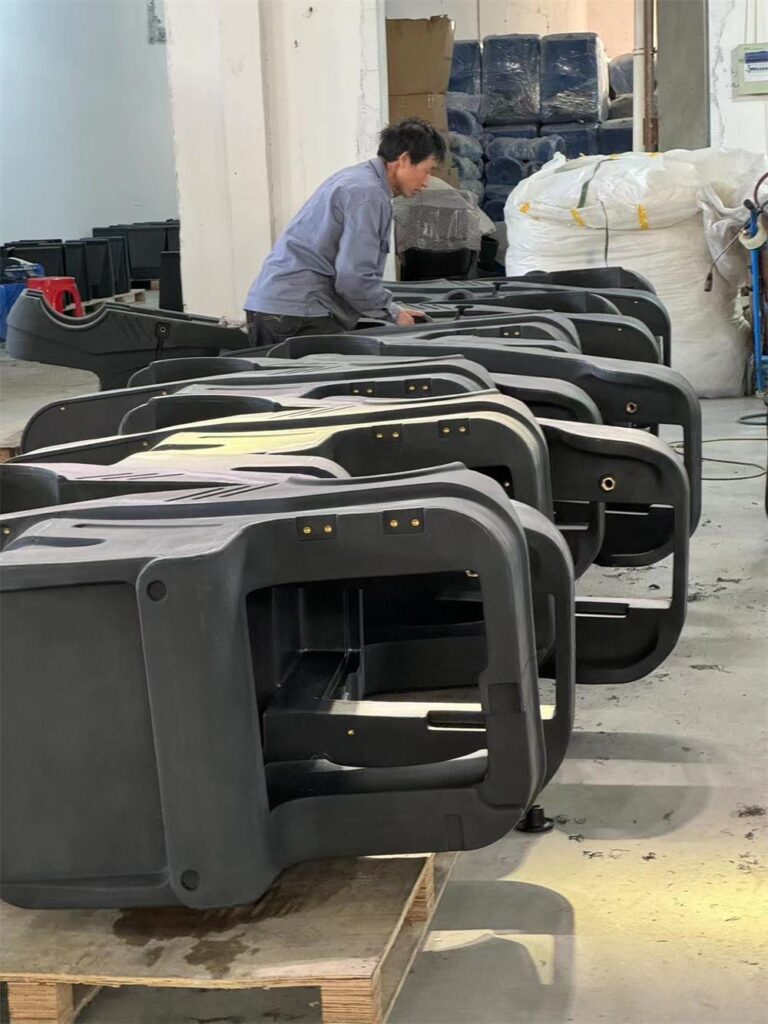
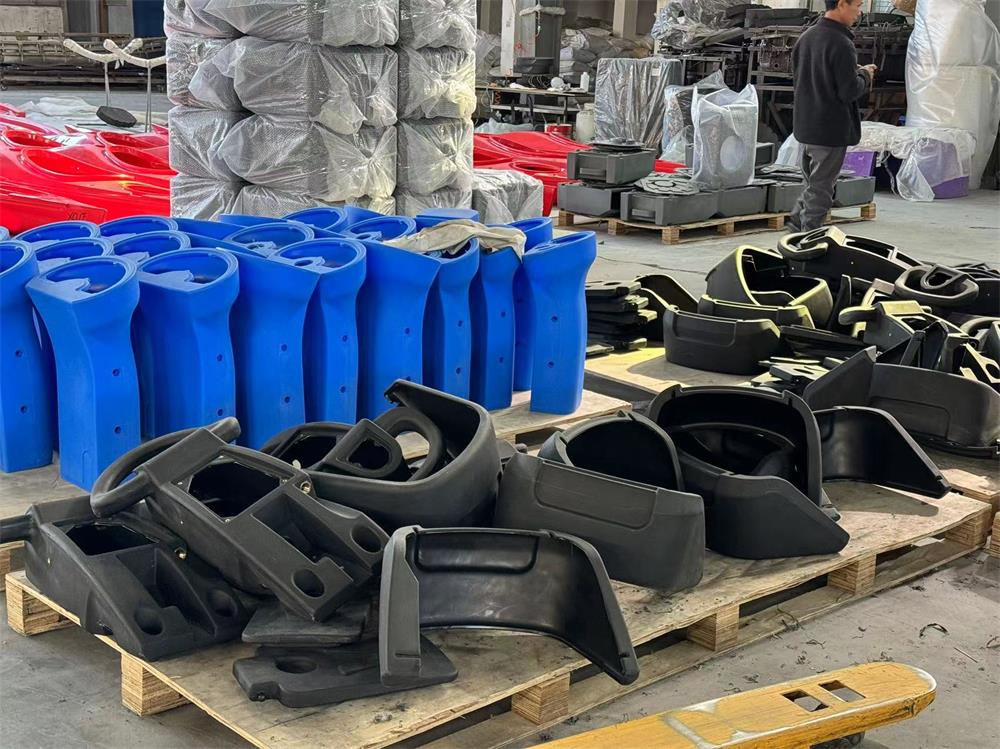
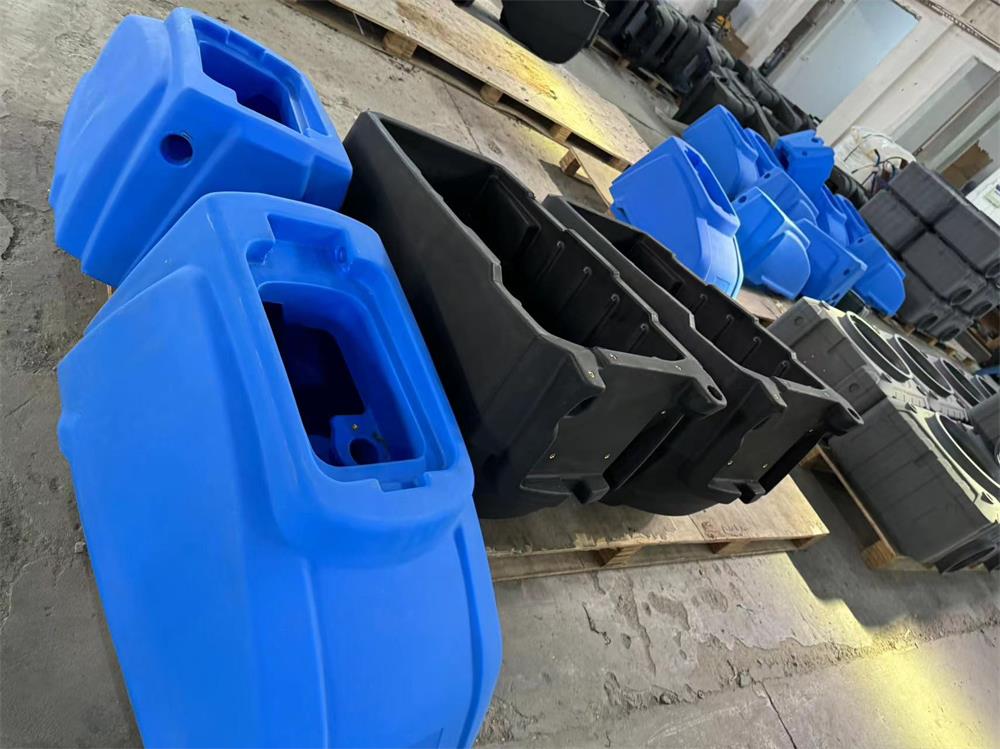
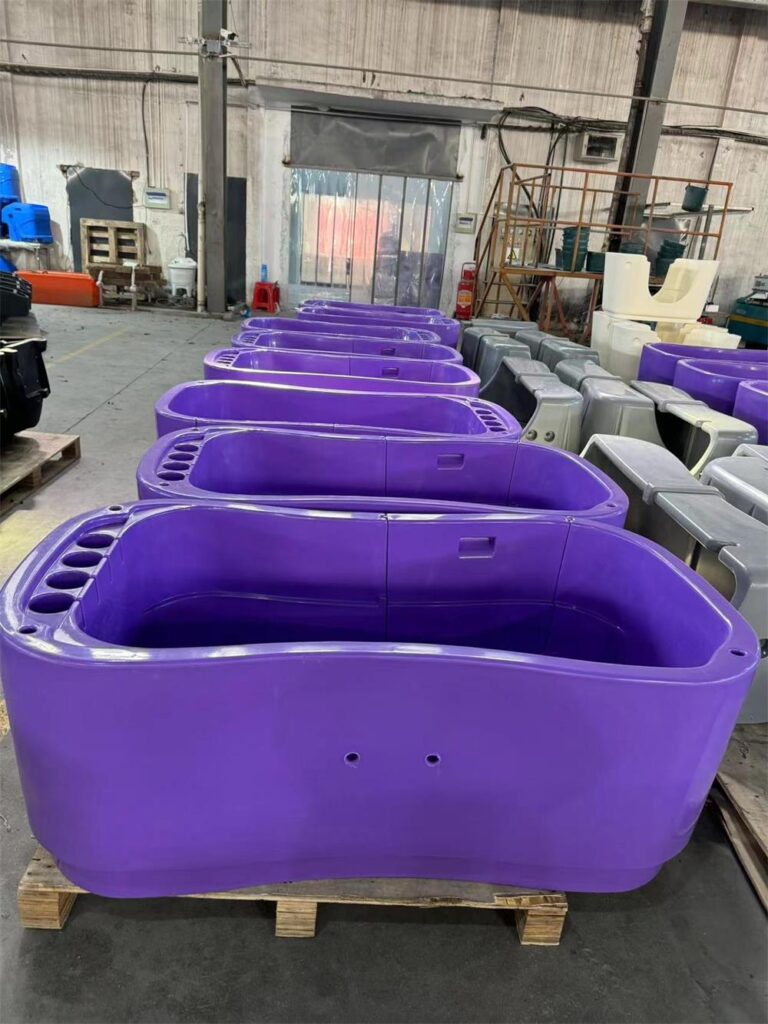
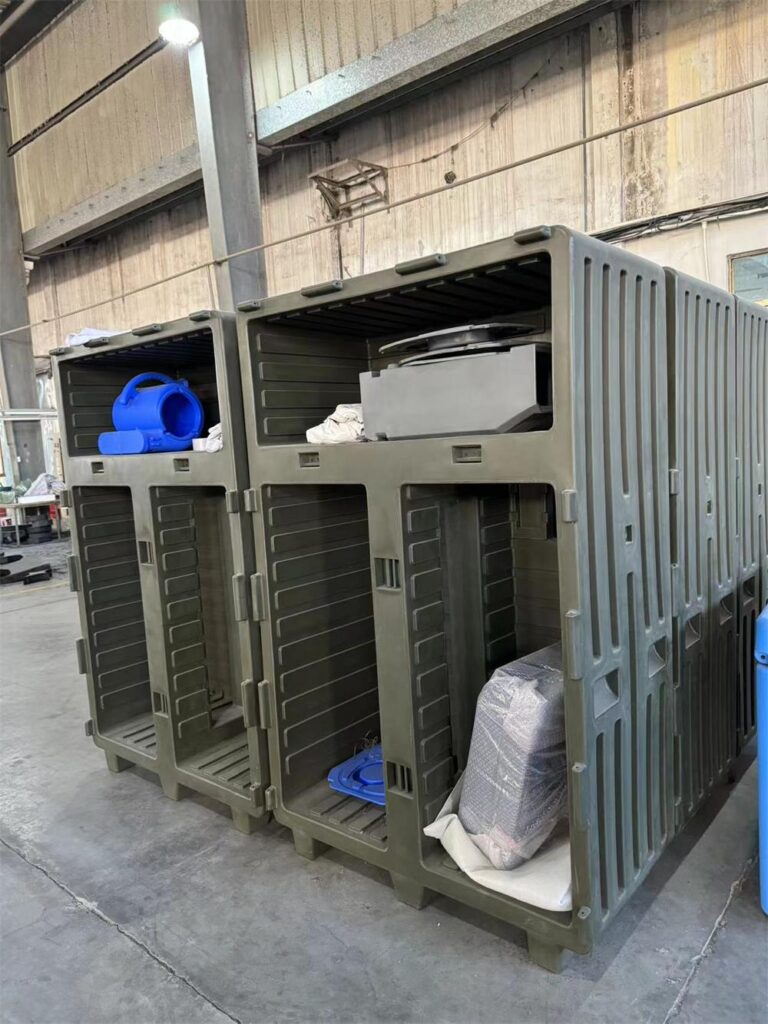
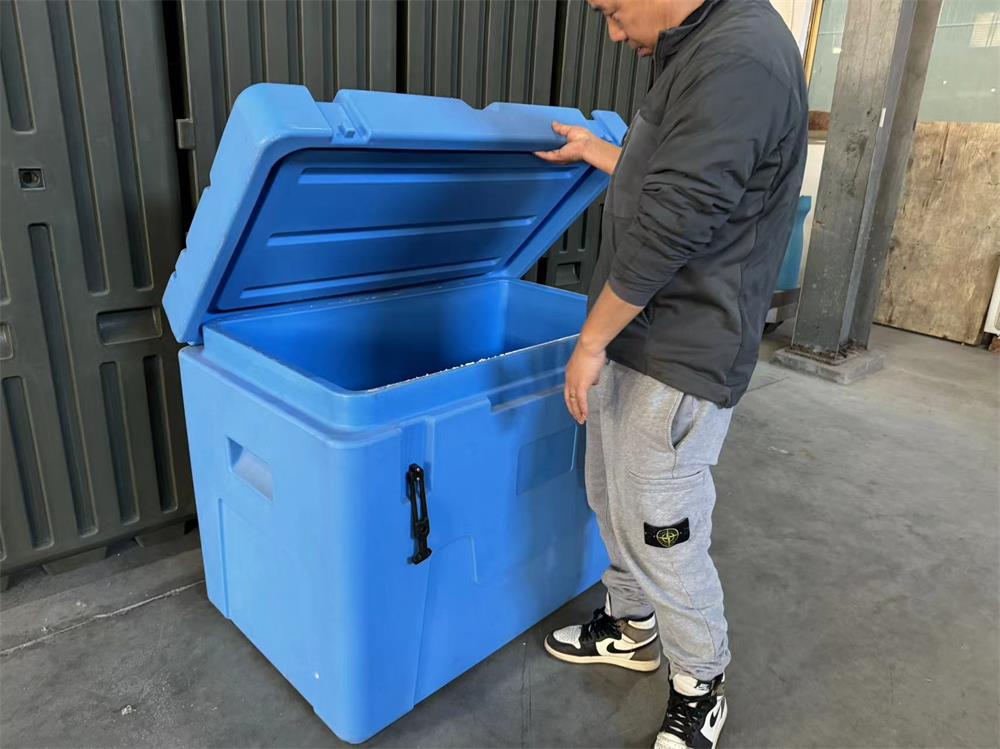
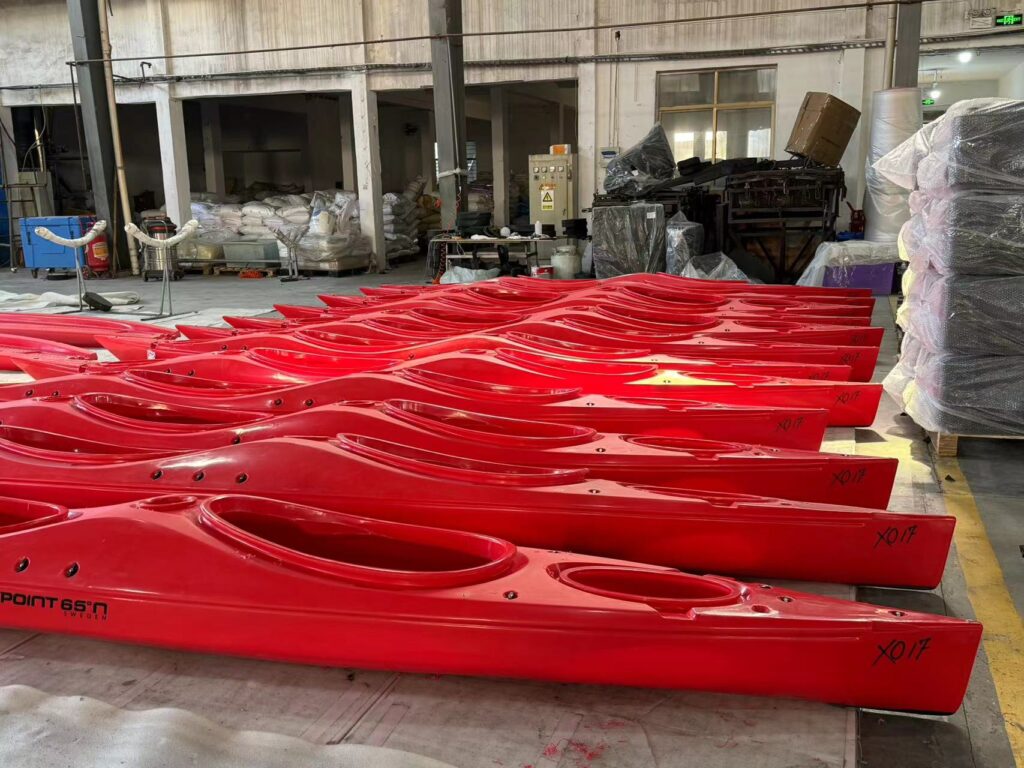
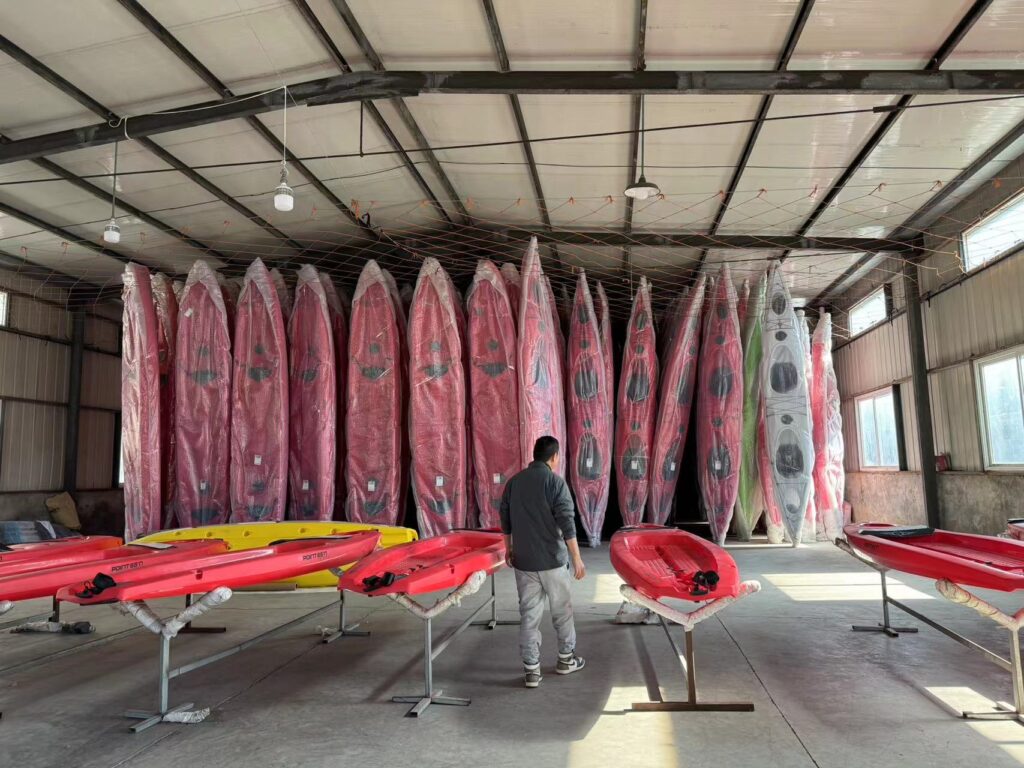
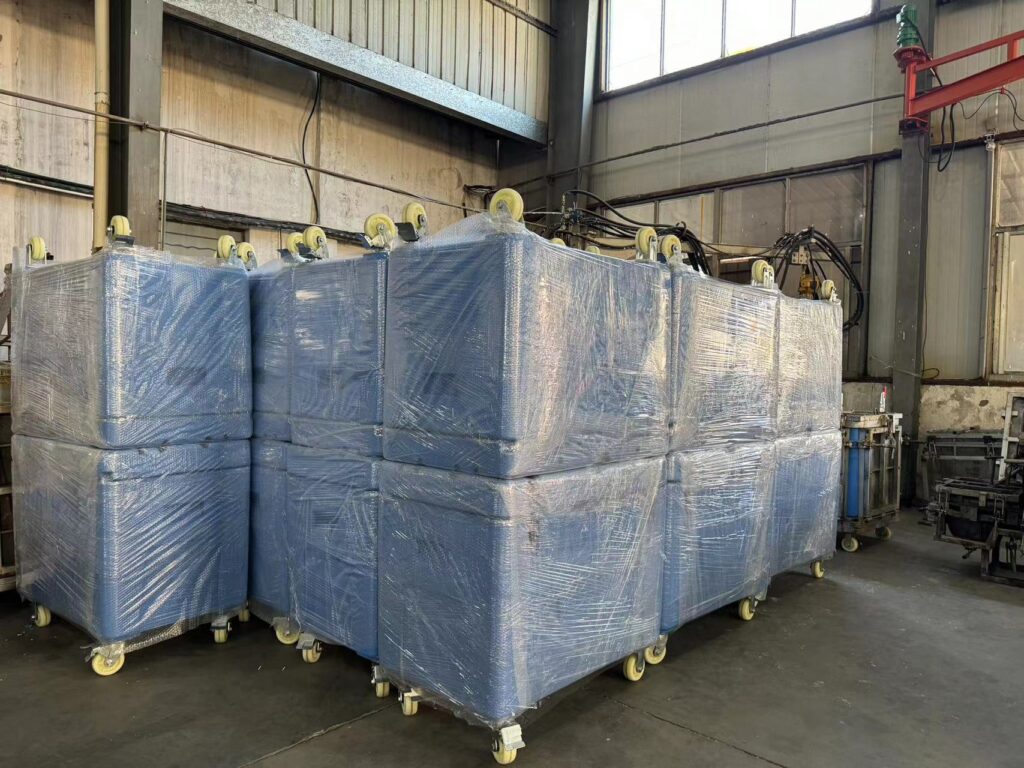
Advantage
Design Advantages
Compared with other mold processes, the rotational molding process provides us with more design space. With the correct design concept, we can combine several parts into a complete mold, which greatly reduces the high assembly costs.
The rotational molding process also includes a series of inherent design thinking methods, such as how to adjust the thickness of the side wall and how to strengthen the external setting. If we need to add some ancillary designs, we can also add strengthening ribs to the design.
The rotational molding process injects designers’ endless imagination into products. Designers can choose the best materials during the production process, including various materials approved by the Food and Drug Administration. The additives put in during the production process can effectively resist external objective factors such as climate attack and static electricity interference. During the design process, the insertion port, threads, handles, inversion devices, and perfect surface design are all one of the highlights. Designers can also create multi-wall molds that can be hollow or filled with foam.
Cost Advantages
When cost also becomes one of the factors we consider, the rotational molding process has more market advantages than other types of processes. When compared with blow molding and injection molding, the rotational molding process can easily produce parts of different sizes within an effective cost range. His mold is also relatively cheap because it doesn’t have an internal core to make. And without the inner core, just a small change can make another model.
Since each part in the production process is finally formed under high temperature and rotation process, unlike those parts formed under heavy pressure, the rotational molding mold does not need to undergo special processing like the injection molding process. Withstand the test of heavy pressure.